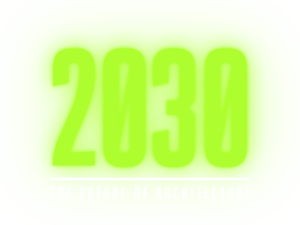
A FREE COURSE TO THE FOREFRONT OF ARCHITECTURE INNOVATION
A FUSION OF SUSTAINABLE DESIGN, HIGH-PERFORMANCE BUILDINGS, AND ARTIFICIAL INTELLIGENCE
JULY 8TH TO 12TH, 2024
ONLINE AND FREE EVENT
JULY 8TH TO 12TH, 2024
ONLINE AND FREE EVENT
By clicking the button, you agree to our Terms of Use and Privacy Policy, including the use of cookies and the sending of communications.
First, what is a Life Cycle?
In order to explain what is a Life Cycle Assessment, first we need to know what is a life cycle. A product’s life cycle refers to all the stages a product goes through, from conception to disposal. The stages of a product’s life cycle can be broadly classified as follows:
- Extraction of raw materials: this stage includes extracting raw materials from nature, such as minerals, oil, wood, and water.
- Production stage: this stage consists of the transformation of raw materials into a finished product via manufacturing processes.
- Distribution: transportation of products from the manufacturer to the point of sale.
- Use: The consumer uses the product during this stage.
- End-of-life: At this stage, the product is disposed of, which can include recycling, reuse, or landfill disposal.
Now, the Main Question: What is Life Cycle Assessment?
Life Cycle Assessment (LCA) is a tool used to assess a product’s or service’s environmental impact throughout its entire lifecycle, from raw material extraction to end-of-life.
Several organizations recognize LCA as a legitimate methodology, including the United Nations Environment Programme (UNEP) and the International Organization for Standardization (ISO). It is also used as a tool for sustainability assessment and decision-making by governments, businesses, and non-governmental organizations (NGOs) all over the world. While LCA has limitations and challenges, it is widely regarded as a valuable and reliable tool for assessing the environmental impact of products and services.
The LCA methodology considers every stage of a product’s lifecycle, including raw material extraction, production, transportation, use, and end-of-life.
LCA evaluates a product’s or service’s environmental impacts, such as greenhouse gas emissions, energy use, water use, and waste generation.
A wide range of information is typically required to perform a life cycle assessment (LCA), such as details about the product or service being evaluated, as well as information about the materials, energy, and other resources used in its manufacture, emissions, wastewater and wastes generated, transportation and logistics, use, and end-of-life.
LCA has many uses, including supply chain management, environmental impact reporting, and product design.
Want to Develop An LCA?
Develop your product life cycle assessment and position your brand toward a sustainable future.
The 4 phases of conducting a Life Cycle Assessment:
The International Organization of Standardization (ISO) has created a specific standard for conducting LCAs, ISO 14040, which provides guidance and the frameworks for conducting an LCA. ISO 14040 is usually combined with ISO 14044, which provides detailed guidance on how to conduct an LCA.
Also, LCA practitioners may follow other standards and norms besides the ISO standards. For instance, if you plan on conducting an LCA for construction products, you might choose to use EN 15804+A2 because it provides detailed guidance on conducting LCA studies for such products.
According to ISO 14040, an Life Cycle Assessment is divided into 4 phases:
- Goal and Scope Definition: This phase involves defining the boundaries and the specific goals and objectives of the assessment, including the products that will be assessed, the functional unit and the reference flow, and the impact categories that will be evaluated.
- Life Cycle Inventory Analysis: Data on the materials, energy, and other resources utilized in the manufacturing, distribution, use, and disposal of the good or service must be gathered and analyzed throughout this phase. This information is used to compile a list of the environmental impacts associated with the product.
- Life Cycle Impact Assessment: This phase uses appropriate impact assessment methods to evaluate the environmental impacts identified in the inventory analysis. Estimating the extent of the impacts and comparing them to relevant benchmarks or standards are part of this process. Also, the impact categories chosen in the Goal and Scope Definition phase are quantified and evaluated in this phase.
- Life Cycle Interpretation: This phase includes interpreting the impact assessment results and communicating them to stakeholders clearly and understandably, usually done via an LCA report and a presentation of the results. This may include developing recommendations for improving the product’s or service’s sustainability.
Here are 5 Benefits of performing an LCA for your products:
- Environmental impact reduction: A life cycle assessment (LCA) can identify environmental hotspots within a product’s lifecycle, allowing potential improvements to be identified and implemented. This can lead to a reduction in the product’s overall environmental impact.
- Resource preservation: LCA can aid in identifying opportunities for resource preservation by spotting areas where resources are being used inefficiently or where alternative materials or processes may be more sustainable.
- Cost savings: Putting an LCA’s recommendations into action can result in cost savings by identifying and implementing more efficient processes and using less expensive, more sustainable materials.
- Risk management: LCA can assist in identifying and assessing potential risks associated with the manufacture, use, and disposal of a product, allowing risk management strategies to be implemented.
- Improved stakeholder relationships: By demonstrating a commitment to sustainability and transparency, LCA can help to strengthen relationships with stakeholders such as customers, regulators, and non-governmental organizations (NGOs). Sustainability and transparency can also result in a better brand reputation and a competitive advantage.
Want to Develop An LCA?
Develop your product life cycle assessment and position your brand toward a sustainable future.
Here are three companies that benefited from performing an LCA:
Nestlé: to better understand the environmental implications of its operations and to find areas for improvement, Nestlé, a multinational food & beverage corporation, has performed LCAs on several of its products. For instance, Nestlé conducted a Life Cycle Assessment on the Nescafe Dolce Gusto coffee pods and discovered that most of the environmental impacts were linked to the processing of the coffee beans and the materials used in the packaging. As a result, Nestle has launched various sustainability efforts based on this knowledge, including buying coffee beans from Rainforest Alliance Certified farms, using recycled materials in its packaging, and collaborating with suppliers to reduce water and energy use in production.
Toyota: Toyota, a major global automotive manufacturer, uses Life Cycle Assessment to assess the environmental effects of their vehicles throughout their lifecycles. As a result, Toyota has discovered that the majority of the environmental impacts of its cars are related to their manufacturing and fuel consumption during the use stage. Based on this finding, Toyota has put into practice many sustainability measures, such as creating hybrid and electric vehicles, using lightweight materials in its cars, and using renewable energy in its production procedures. Also, these initiatives are a part of their long-term goal of becoming carbon neutral until 2050, which is a goal in line with the Paris Agreement.
Roca Brasil Cerámica: Roca Brasil Cerámica is a Brazilian manufacturer of porcelain tiles. They conducted an LCA to implement sustainable practices and help customers obtain sustainable building certifications, such as LEED. As a result, they found that the materials with more significant environmental impacts were petroleum coke and natural gas, two fuels used in the manufacturing line. So, in 2021, they ended up substituting petroleum coke, a non-renewable fuel derived from oil, with biomass, a renewable energy source.
How hard is it to conduct a Life Cycle Assessment?
Depending on the specific goals and objectives of the assessment, as well as the product’s characteristics, conducting a Life Cycle Assessment (LCA) can be a complex and time-consuming process.
LCA requires the gathering and analysis of a wide range of data on the materials, energy, and other resources used in the product’s or service’s production, transportation, use, and disposal, as well as the assessment of the environmental impacts associated with these activities.
Several factors can affect the complexity of a Life Cycle Assessment, including the size and scope of the product being assessed, the availability and quality of data, and the specific impact categories and methods used in the assessment. LCAs are generally more complex for goods or services with long or complex supply chains or those involving multiple stages of production or use.
However, various resources and tools are available to assist businesses and organizations in conducting LCAs. For example, numerous data collection and analysis software tools and databases are available, as well as various LCA standards and guidelines that guide best practices for conducting LCAs in different sectors.
Overall, while conducting an LCA can be a complex and time-consuming process, it can also be a valuable tool for understanding and improving the sustainability of a product or a brand.
How much time does it take to conduct a life cycle assessment?
The time required to complete an LCA can vary greatly depending on the specific goals and objectives of the evaluation. It can also vary depending on the characteristics of the product or service being evaluated. LCA is a complex and time-consuming process that entails gathering and analyzing a wide range of data on the materials, energy, and other resources used in the production, transportation, use, and disposal of a product or service, as well as assessing the environmental impacts associated with these activities.
Various resources and tools are available to assist businesses and organizations in conducting LCAs, which help organize data, calculate impact, and, generically speaking, reduce the required time to perform an LCA.
Overall, while conducting an LCA can be a complex and time-consuming process, it can help your company stay ahead of your competitors and create a competitive advantage from the sustainability point of view.
Want to Develop An LCA?
Develop your product life cycle assessment and position your brand toward a sustainable future.
Are Life Cycle Assessments required to be critically reviewed?
Although life cycle assessments (LCAs) are not typically required to be critically reviewed, it is generally regarded as good practice to subject LCAs to some form of review or verification to ensure the credibility and reliability of the results. The type of review or verification process used will be determined by the assessment’s specific goals and objectives, as well as the characteristics of the product or service being evaluated.
A few approaches can be used to review or verify a Life Cycle Assessment, including internal review, peer review, and third-party verification. An internal review is the evaluation of an LCA by the team or organization that conducted the assessment. In contrast, peer review is the evaluation of an LCA by other experts or practitioners in the field. Finally, third-party verification entails having an independent, unbiased third-party review of an LCA.
The need for a critical review may vary depending on the goal of the LCA. For instance, LCAs used to create Environmental Product Declarations (EPDs) are typically required to be critically reviewed by a third party to ensure their accuracy and reliability. This “verification” process helps to ensure that the LCA and EPD meet specific quality standards and that the Life Cycle Assessment results are founded on sound scientific principles.
While it is not typically required by law or regulation, subjecting LCAs to some form of review or verification is generally considered good practice to ensure the credibility and reliability of the results. In addition, a critical review can boost trust in the LCA by providing that it is founded on sound scientific principles and best practices.
For how long is a Life Cycle Assessment valid?
In general, changes in the product or service being evaluated and the environmental impacts associated with the product or service impact the validity of an LCA. For example, if the product materials, energy consumption, or other characteristics change significantly, the LCA may no longer be valid. Similarly, if the environmental impacts of the product change significantly (e.g., changes in energy prices or emission factors), the LCA may no longer be valid.
An LCA should be re-evaluated regularly to ensure that it remains relevant and accurate. The frequency of re-evaluation will be determined by the assessment’s specific goals and objectives and the product’s characteristics.
How can I start my Life Cycle Assessment with UGREEN?
To start your Life Cycle Assessment with UGREEN, you will need to follow these steps:
- Contact UGREEN: the first step is to get in touch with UGREEN to discuss your goals and how an LCA can help your brand. You can do this by scheduling a meeting here.
- Schedule a meeting with the teams involved: once the LCA project starts, the teams must meet because a variety of confidential information is required for an LCA. So all teams involved can be in line with what’s happening, what information they should provide, and how they can help provide other necessary information.
- Conducting the LCA: the UGREEN team will ask for, compile and use the information to assess the environmental impacts of the LCA. In addition, a confidential report containing all assumptions and methodologies used in the LCA will be written.
- Critical review: in this step, a third party will read the LCA report and check for errors, invalid methodologies, and missing information to maximize the transparency and reliability of the report. At the end of this step, the report will contain the critical reviewer’s signature to ensure the LCA’s legitimacy. This step is optional but highly recommended.
- Presentation of results: the final Life Cycle Assessment report will be delivered to you (with the critical reviewer’s signature) so that the LCA can be used for improvement.
So start your process now with UGREEN!
Want to Develop An LCA?
Develop your product life cycle assessment and position your brand toward a sustainable future.
Need to develop it in the Portuguese language? Go to our Portuguese page by clicking here.