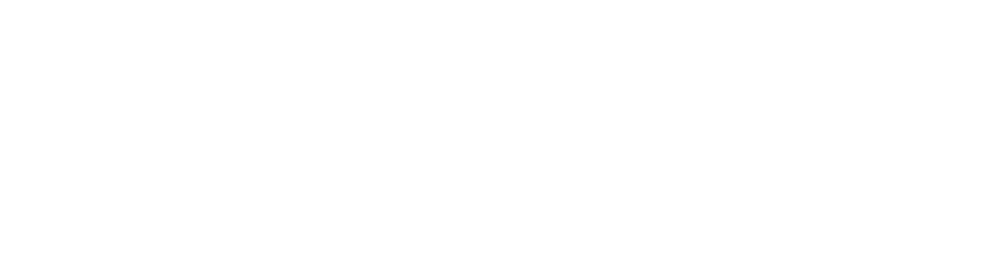
We transform sustainability into a smart investment, with real and proven results.
Imagine your dream home: sleek, modern, perhaps with curves that defy traditional construction logic. Now, picture it coming to life layer by layer, from the ground up, in just days. Welcome to the revolutionary world of 3D printed houses, where the future of homebuilding is being extruded through a nozzle, layer by layer. This isn’t science fiction; it’s the reality of today’s construction technology, pushing the boundaries of what’s possible in design, efficiency, and sustainability.
How Does 3D Printing House Work?
At its core, 3D printing houses involves a gigantic printer, but instead of ink, it uses concrete or other materials, crafting walls and structures from digital designs. It’s like building with LEGO, but each block is precisely placed by robotic arms with unerring accuracy.
The Process of 3d Printing, Simplified:
- Design: Every build starts in the digital realm. Architects create models using sophisticated software, mapping out every nook and cranny.
- Preparation: The ground is prepped, much like traditional construction, ensuring a stable foundation for the 3D-printed structure.
- Printing: Layer by layer, the printer lays down material, following the digital blueprint to the letter. Walls rise from the ground, with spaces for windows, doors, and all the utilities you’d expect in a modern home.
- Finishing Touches: Once the printing is complete, human hands take over for the finer points—electrical, plumbing, and those personal touches that make a house a home.
Environmental Impact of 3d Printing and Sustainability
One of the most compelling aspects of 3D printed houses is their potential for sustainability. But how green is this technology, really?
Pros:
- Reduced Waste: Traditional construction can be wasteful, but 3D printing uses material with precision, slashing the leftovers that end up in landfills.
- Sustainable Materials: Innovations abound, with some printers using eco-friendly materials like recycled plastics or natural fibers, turning waste into walls.
- Energy Efficiency: The design freedom of 3D printing allows for structures that are inherently more energy-efficient, with better insulation and reduced heating and cooling costs.
Cons:
- Carbon Footprint: The energy consumed by the printers and the production of printing materials can offset some of the environmental benefits.
- Material Limitations: Currently, most printers use concrete-based materials, which have a significant environmental impact. More sustainable options are emerging, but they’re not yet widespread.
The Verdict:
It’s a mixed bag. While 3D printing in construction has the potential to revolutionize sustainable building, the technology and materials need to evolve further to fully realize this promise.
This peek into the world of 3D printed houses only scratches the surface. The technology is evolving, pushing us towards a future where homes are built faster, cheaper, and greener. Stay tuned as we dive deeper into this fascinating topic, exploring the nuts and bolts of 3D printed homes, their cost implications, and the extraordinary designs that are only possible with this cutting-edge technology.
Cost Analysis of 3d Printing: Affordability and Market Accessibility
Welcome to the brass tacks of 3D printed houses: the cost. Are these futuristic homes only within reach for the Tony Starks of the world, or can the average Joe and Jane dream of printing their nest? Let’s break it down.
Breaking Down the Costs of 3d Printing
Initial Investment:
- Printer Price Tag: The heart of the operation, a construction-grade 3D printer, can set you back anywhere from $250,000 to over $1 million. However, this is a one-time investment that’s spread over countless builds.
- Material Matters: Concrete, the go-to material, is relatively cheap, but innovative, more sustainable materials can add to the cost. On the flip side, precise material use reduces waste, trimming costs.
Operational Savings:
- Labor Love: Reduced manpower requirements lower the overall construction bill significantly. Fewer hands on deck, but no compromise on the build’s integrity.
- Time is Money: Faster build times mean less money spent on site preparation, security, and other time-dependent costs.
The Price Tag on a 3D Printed House
Let’s put numbers on the table. While traditional homes in the U.S. can cost anywhere from $100 to $200 per square foot, 3D printed options promise significant savings. Early projects have shown costs as low as $10 per square foot for the printing process, with overall costs ranging significantly based on design complexity, location, and finishing touches.
Cost Comparison
Construction Type | Cost per Square Foot | Time to Build | Labor Needed |
---|---|---|---|
Traditional | $100 – $200 | 6 – 12 months | Many |
3D Printed | $10 – $50 | Days – Weeks | Few |
Accessibility: Not Just a Rich Man’s Game
The promise of 3D printed houses extends beyond saving dollars; it’s about democratizing construction. Affordable housing projects are popping up, showcasing the potential to quickly provide homes for those in need. With costs potentially slashed by up to 50%, we’re looking at a future where quality housing is within reach for a broader segment of the population.
The affordability and efficiency of 3D printed houses make them a compelling option for future housing needs. But, as with any emerging technology, there’s a balance to be struck between cost, sustainability, and practicality. As we move forward, the industry’s challenge will be to make these homes not just financially accessible but also widely accepted and loved. Stay tuned as we continue to explore this fascinating journey from blueprint to reality, one layer at a time.
Continuing our exploration into the world of 3D printed houses, let’s delve into design and aesthetics, a realm where this technology truly shines, offering possibilities that traditional construction methods can only dream of.
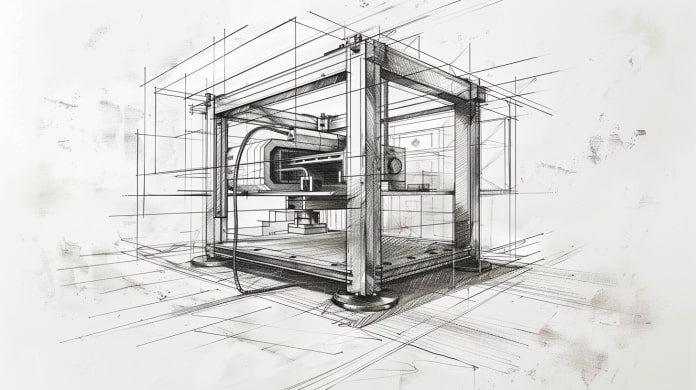
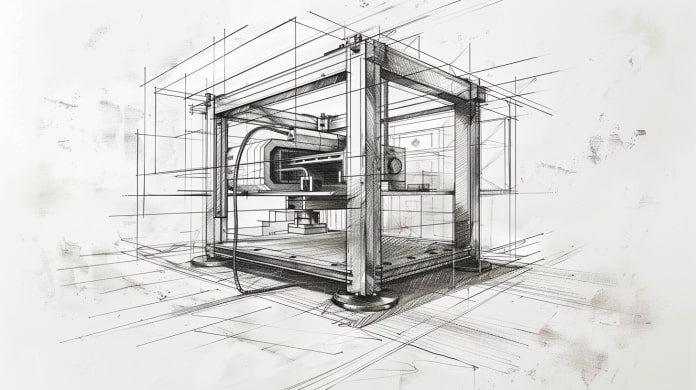
Design and Aesthetics in 3D Printed Houses
The allure of 3D printed houses isn’t just in their innovative construction method or the potential cost savings; it’s also in their unprecedented design flexibility. Imagine homes that curve, swoop, and undulate—designs that were once prohibitively expensive or even impossible to construct using traditional methods.
The Freedom of Form of 3d Printing
Curves and More:
- Organic Shapes: With 3D printing, architects are no longer constrained by straight lines and right angles unless they choose to be.
- Customization: Each house can be as unique as its owner, with bespoke features that cater to individual preferences and land constraints.
Architectural Innovations: A Quick Look with 3d Printing
- The Printed Mansion: Envision a sprawling estate with flowing walls that mimic natural landscapes, all made possible with concrete printing.
- Eco-Friendly Abodes: Compact, energy-efficient homes designed with sustainability at their core, utilizing natural light and thermal dynamics for comfort without the carbon footprint.
- Artistic Flair: Structures that double as large-scale art installations, challenging our perceptions of what a home can be.
Design Possibilities vs. Traditional Constraints
Feature | 3D Printed Houses | Traditional Houses |
---|---|---|
Curved Walls | Easily achievable | Difficult and costly |
Custom Features | Unlimited | Limited by cost |
Construction Time | Days to weeks | Months to years |
Sustainability | High potential | Variable |
Cost | Lower overall | Higher overall |
Global Examples of 3D Printed Houses
The global landscape of 3D printed houses showcases a tapestry of innovation, each project highlighting a unique benefit or feature. From affordable housing in Latin America to luxury villas with organic designs, the versatility of 3D printing is on full display.
Highlighting Significant Projects of 3d Printing
- Europe’s First: A community of 3D printed homes in the Netherlands, combining cutting-edge design with functionality and sustainability.
- Disaster Relief Housing: In disaster-prone areas, 3D printed homes offer a quick, durable solution for those affected by natural calamities.
- Affordable Urban Housing: Cities struggling with housing shortages are looking to 3D printing to provide cost-effective, sustainable options for residents.
The Pros and Cons: A Balanced View
While the potential of 3D printed houses is immense, it’s important to approach this technology with a balanced perspective.
Advantages of 3d Printing:
- Innovative Design: The sky’s the limit when it comes to what can be achieved.
- Rapid Construction: Build times are drastically reduced.
- Reduced Costs: Significant savings on labor and materials.
Challenges of 3d Printing:
- Public Perception: Overcoming skepticism about the durability and safety of these homes.
- Regulatory Hurdles: Ensuring that 3D printed houses meet all local building codes and standards.
- Material Limitations: Expanding the range of sustainable materials available for use in 3D printing.
Conlusion: 3d Printing
In essence, 3D printed houses stand at the forefront of revolutionizing the construction industry, offering a blend of sustainability, affordability, and unparalleled design flexibility. This emerging technology promises to tackle housing crises, redefine architectural norms, and make eco-friendly homes more accessible. Despite facing regulatory and perceptual challenges, the trajectory of 3D printing in construction points towards a future where innovative, personalized homes become the norm. As the technology matures and overcomes existing hurdles, it beckons a new era of building that could very well redefine what it means to call a place home. The journey of 3D printed houses from novelty to mainstream acceptance illustrates a pivotal shift in construction, poised to leave a lasting impact on how we live.
If you want o learn about our consultancies in Portuguese language, click here.
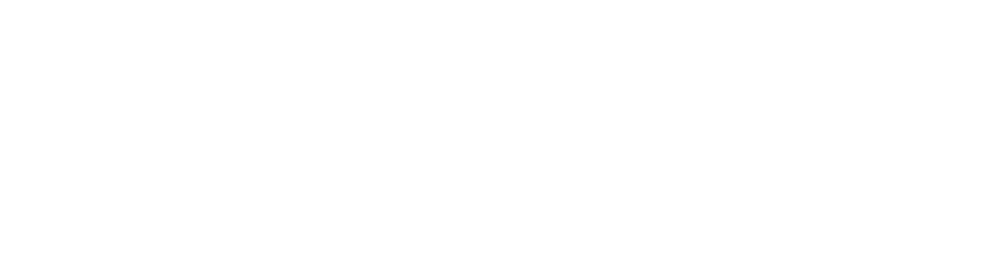
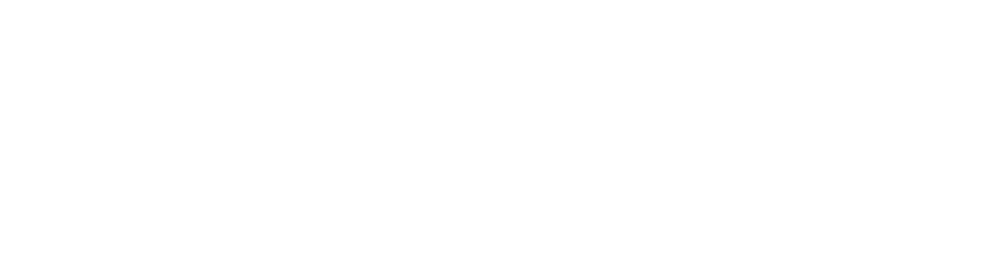
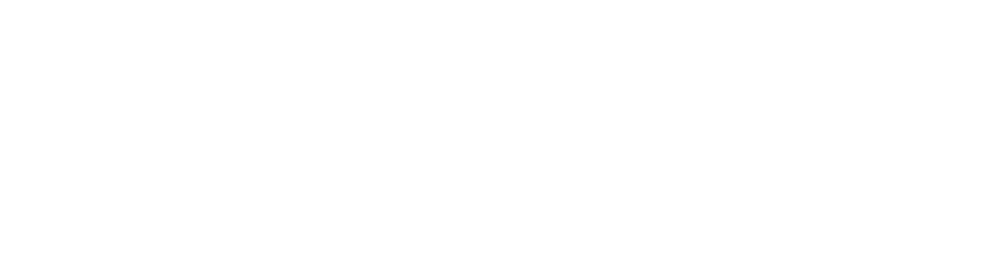
We transform sustainability into a smart investment, with real and proven results.